ابزارهای مورد نیاز در جوشکاری آرگون | تجهیزات جوشکاری TIG
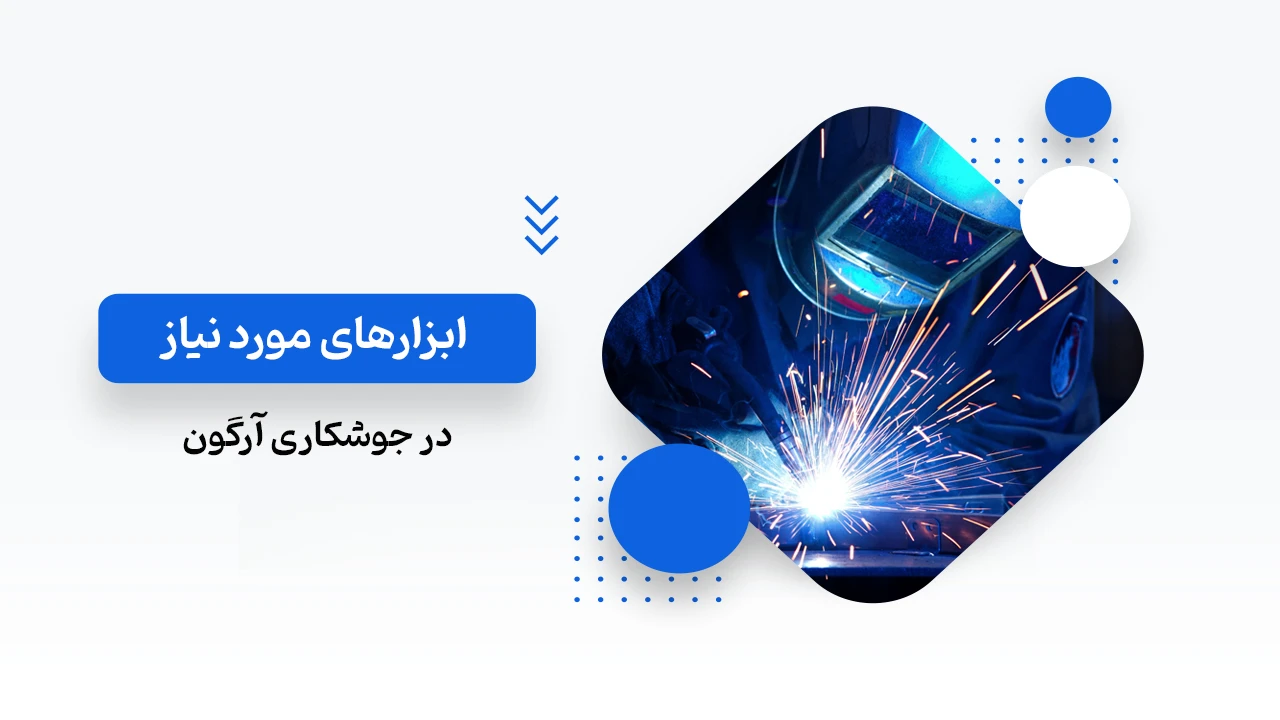
دسترسی سریع به محتوای این مطلب
یکی از روش های ساخت و اتصال مواد مختلف به یکدیگر، جوشکاری است. در این نوع عملیات مواد با کمک حرارت بسیار زیاد و در بعضی مواقع بدون نیاز به وارد کردن فشار، به یکدیگر اتصال پیدا می کنند. جوشکاری، عملیاتی است که با ذوب کردن قسمتی از فلزات، یک اتصال دائمی بین آنها به وجود می آید.
ذکر این نکته ضروری است که برای جوشکاری از مواد گوناگونی استفاده می شود. یکی از مواد مورد استفاده، گاز آرگون است که در این مقاله سعی داریم در مورد ابزارآلات جوشکاری آرگون اطلاعاتی را در اختیار شما قرار دهیم. پس با ما همراه باشید.
فایل صوتی
فایل ویدئویی
جوشکاری آرگون (TIG) چیست؟
جوشکاری آرگون یا Tungsten Inert Gas یکی از روش های پرکاربرد جوشکاری است که در آن از یک قوس الکتریکی برای ذوب فلز و ایجاد اتصال استفاده می شود. این روش به دلیل کیفیت بالای جوش، کنترل دقیق و قابلیت استفاده برای انواع فلزات، بسیار محبوب است.
در این روش، یک الکترود تنگستنی که در برابر حرارت بسیار مقاوم است، به عنوان منبع حرارت عمل می کند. با ایجاد یک قوس الکتریکی بین الکترود تنگستنی و قطعه کار، حرارت بسیار بالایی تولید می شود که باعث ذوب شدن فلز در محل اتصال خواهد شد. برای جلوگیری از اکسیداسیون فلز مذاب، از یک گاز بی اثر مانند آرگون استفاده می شود. این گاز یک محیط محافظ ایجاد می کند تا فلز مذاب در تماس با هوا قرار نگیرد و کیفیت جوش بهبود یابد.
به عبارت دیگر یکی از شیوه های اتصال فلزات به یکدیگر، عملیات جوشکاری است. جوشکاری آرگون یا جوشکاری تیگ، همان جوش دادن قوس تنگستن در کنار گاز محافظ است. جوشکاری آرگون با استفاده از گاز آرگون انجام می شود. این گاز در دسته گازهای بی خطر قرار می گیرد و مسمومیتی برای انسان ایجاد نمی کند. جوشکاری آرگون یا TIG با کمک یک الکترود غیرمصرفی با جنس تنگستن انجام می شود.
تنگستن به دلیل دمای ذوب بالا با هدف ایجاد قوس همراه با گاز آرگون، به منظور محافظت از جوش مورد استفاده قرار می گیرد. معمولا در این شیوه، سیم جوش برای ذوب شدن و پر کردن فضای منطقه جوشکاری کاربرد دارد.
در گذشته قوس و حوضچه مذاب به صورت کامل قابل مشاهده بودند، که با گذر زمان با استفاده از اتمسفر و قرار دادن قوس و حوضچه در مقابل آن یک جوشکاری ایده آل را انجام می دادند. با تولید الکترودها این نوع شیوه محافظتی در جوشکاری، غیر امن و منتفی اعلام شد. در دهه 1930 با ابداع الکترود تنگستن و وجود گاز خنثی، جوشکاری محافظت شده با گاز در چرخه کاری قرار گرفت.
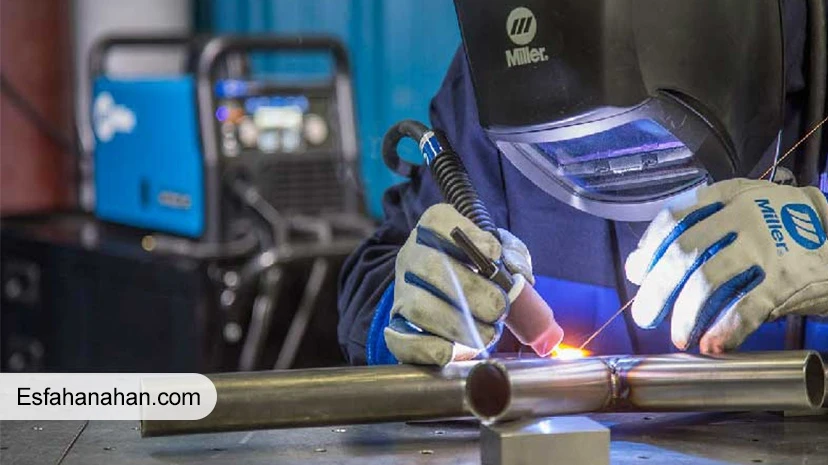
ابزار مورد نیاز در جوشکاری آرگون
اجرای فرایند جوشکاری، نیازمند یک سری لوازم و ابزارهای خاص است. برخی از این وسایل در تمامی جوشکاری ها مشترک هستند. جوشکاری آرگون یکی از فعالیت های صنعتی مهم است، که به ملزومات و ابزارهای مخصوصی نیاز دارد . جدول ابزار جوشکاری آرگون به صورت زیر است:
لوازم جوشکاری آرگون | شرح وظیفه |
---|---|
منبع تغذیه | تأمین جریان الکتریکی مورد نیاز برای ایجاد قوس الکتریکی و ذوب فلز |
سیلندر گاز محافظ | حاوی گاز آرگون که به عنوان محیط محافظ برای جلوگیری از اکسیداسیون فلز مذاب عمل می کند |
رگولاتر و فلومتر | تنظیم فشار و دبی گاز خروجی از سیلندر |
شیلنگ و بست های گاز | اتصال سیلندر گاز به مشعل و هدایت گاز به محل جوشکاری |
تورچ یا مشعل | هدایت جریان الکتریکی به الکترود تنگستن و کنترل جریان گاز محافظ |
کابل اتصال | اتصال منبع تغذیه به مشعل و قطعه کار |
الکترود تنگستن | ایجاد قوس الکتریکی و ذوب فلز |
سیم جوش | پر کردن حوضچه جوش و تقویت اتصال |
انبر اتصال | ثابت نگه داشتن قطعه کار |
انبر جوش | نگه داشتن الکترود تنگستن و کنترل طول آن |
منبع تغذیه (Power Source):
اولین و مهم ترین ابزار مورد استفاده در جوشکاری آرگون، تهیه منبع تغذیه است. منبع تغذیه می تواند از هر دو نوع مولد برق جریان مستقیم یا DC و جریان متناوب یا AC استفاده کند. منبع های تغذیه معمولا ترانسفورماتور یکسو ساز یا ژنراتورها هستند. ولتاژ و آمپر این منبع را می توان بر اساس نوع فلز، ضخامت قطعه کار و نوع جوش تنظیم کرد.
انواع منبع های تغدیه عبارتند از:
- جریان مستقیم (DC): برای جوشکاری اکثر فلزات، به ویژه آلومینیوم و فولاد ضد زنگ، مناسب تر است.
- جریان متناوب (AC): برای جوشکاری آلومینیوم به دلیل خاصیت تمیزکنندگی قوس، بیشتر استفاده می شود.
منبع تغذیه باید بتواند جریان و ولتاژ ثابتی را تولید کند، تا قوس الکتریکی پایدار و یکنواخت ایجاد شود. امکان تنظیم ولتاژ و جریان خروجی در منبع تغذیه، برای تطبیق با انواع فلزات، ضخامت قطعه کار و نوع جوش ضروری است.
منبع تغذیه باید در برابر نوسانات برق مقاوم باشد، تا از اختلال در فرآیند جوشکاری جلوگیری شود. توجه داشته باشید که وجود سیستم های حفاظتی مانند محافظت در برابر اتصال کوتاه و برق گرفتگی، ایمنی جوشکار را تضمین می کند.
منبع تغذیه از سه جزء اصلی ترانسفورماتور، یکسو کننده و مدار کنترل تشکیل می شود. ترانسفورماتور ولتاژ ورودی را به ولتاژ مورد نیاز برای جوشکاری تبدیل می کند. یکسو کننده جریان متناوب را به جریان مستقیم و مدار کنترل ولتاژ و جریان خروجی را تنظیم می کند.
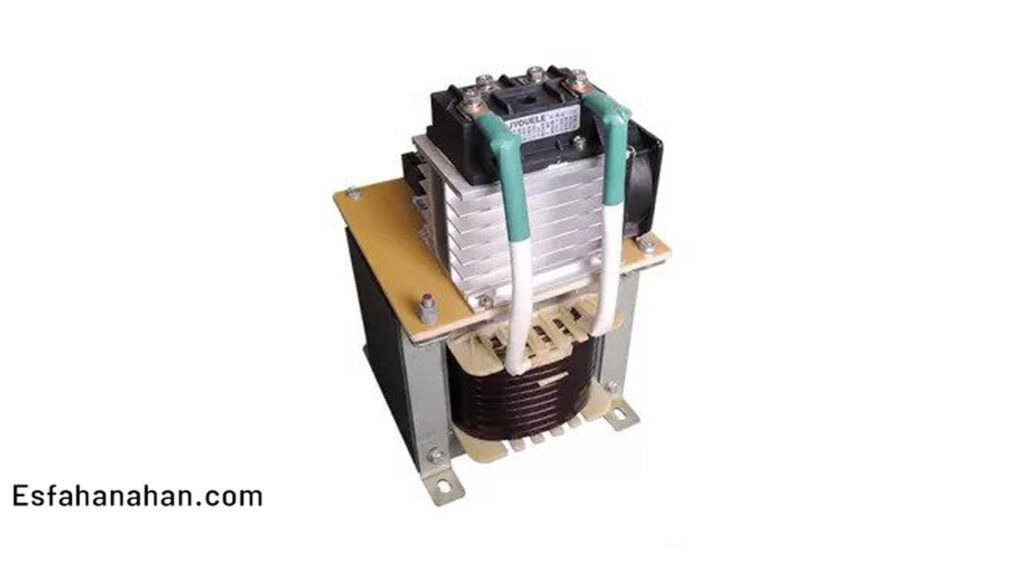
سیلندر گاز محافظ
سیلندر گاز محافظ یکی از اجزای ضروری در فرایند جوشکاری، به ویژه جوشکاری آرگون (TIG) است. این سیلندرها حاوی گازهای بی اثر مانند آرگون هستند، که نقش محافظتی حیاتی را در حین جوشکاری ایفا می کنند. گاز موجود در سیلندر با ایجاد یک محیط محافظ اطراف قوس جوش، از تماس فلز مذاب با هوا و اکسید شدن آن جلوگیری می کند. این امر منجر به تولید جوش هایی با کیفیت بالاتر و بدون عیوب می شود.
گاز محافظ به پایداری قوس جوش کمک کرده و از نوسانات و قطع شدن آن جلوگیری می کند. در این سیلندر گاز محافظ با ایجاد یک لایه پوششی، از پاشش ذرات مذاب و ایجاد سرباره جلوگیری می کند.
سیلندرهای گاز معمولاً از جنس فولاد ساخته و برای تحمل فشار بالا طراحی شده اند. فشار گاز درون سیلندر بسته به نوع گاز و کاربرد آن متفاوت است. در جوشکاری آرگون،این فشار معمولا بین 150 تا 200 بار است.
رگولاتر و فلومتر
رگولاتور و فلومتر دو ابزار بسیار مهم و حیاتی در فرآیند جوشکاری آرگون هستند، که به منظور کنترل و تنظیم دقیق جریان گاز محافظ مورد استفاده قرار می گیرند. این دو ابزار در کنار هم کار می کنند تا اطمینان حاصل شود که مقدار مناسب گاز محافظ با فشار صحیح به محل جوشکاری هدایت می شود.
رگولاتور (Pressure Regulator)، وظیفه کاهش فشار بالای گاز درون سیلندر به فشار کاری مورد نیاز برای جوشکاری و تنظیم دقیق این فشار را برعهده دارد. رگولاتور دارای یک دیافراگم است که با تغییرات فشار گاز وارد شده از سیلندر، حرکت کرده و در نتیجه شیر کنترل را باز یا بسته می کند. به این ترتیب، فشار خروجی گاز به صورت ثابت و در محدوده تنظیم شده حفظ می شود. با استفاده از یک پیچ تنظیم، می توان فشار خروجی گاز را بین 3 تا 7 بار (بسته به نوع جوشکاری و فلز) تنظیم کرد.
وظیفه فلومتر (Flowmeter) اندازه گیری و تنظیم دقیق میزان جریان گاز خروجی از رگولاتور است. فلومتر دارای یک لوله شیشه ای مدرج است که داخل آن یک شناور وجود دارد. با افزایش جریان گاز، شناور بالاتر می رود و بر روی مقیاس مدرج، میزان جریان گاز قابل مشاهده است. با چرخاندن یک پیچ تنظیم، می توان جریان گاز را به مقدار دلخواه رساند.
تنظیم دقیق جریان گاز برای دستیابی به یک حوضچه جوش پایدار و با کیفیت بسیار مهم است. جریان کم گاز ممکن است باعث اکسید شدن فلز جوش شود و جریان زیاد گاز نیز ممکن است باعث سرد شدن سریع جوش و ایجاد ترک شود.
شیلنگ و بست های گاز
شیلنگ و بست های گاز دو جزء کوچک اما بسیار مهم در فرایند جوشکاری آرگون هستند. این دو قطعه به ظاهر ساده، نقش حیاتی در انتقال گاز محافظ از سیلندر به مشعل و ایجاد یک محیط محافظ پایدار در اطراف قوس جوش را بر عهده دارند.
شیلنگ گاز، یک لوله انعطاف پذیر است که برای هدایت گاز محافظ از سیلندر به مشعل جوشکاری استفاده می شود. این شیلنگ معمولاً از مواد مقاوم در برابر حرارت و فشار ساخته شده تا بتواند شرایط سخت محیط جوشکاری را تحمل کند. به همین دلیل معمولاً از لاستیک تقویت شده با الیاف مصنوعی یا فلز ساخته می شوند تا مقاومت آن ها در برابر فشار و حرارت بالا باشد. انعطافپذیری مناسب شیلنگ به جوشکار اجازه می دهد، تا مشعل را به راحتی در موقعیت های مختلف قرار دهد.
بست های گاز، قطعاتی هستند که برای اتصال محکم شیلنگ به سیلندر و مشعل استفاده می شوند. این بست ها باید به گونه ای طراحی شوند که از نشتی گاز جلوگیری کنند. بست های گاز در انواع مختلفی مانند بست های پیچشی، فنری و بست های سریع بازشو وجود دارند. بست گاز نقش بسیار مهمی در ایمنی جوشکاری دارد. یک بست شل یا معیوب می تواند باعث نشت گاز و ایجاد خطر شود.
تورچ یا مشعل
این قطعه یکی از ابزارهای مکانیکی در جوشکاری آرگون است، که در انواع مختلفی تولید و در اختیار جوشکاران قرار می گیرد. تورچ یا مشعل (torch)، هدایت جریان برق از رکتیفایر (rectifier) به کمک کابل اتصال به سمت الکترود تنگستن و گاز محافظ را انجام می دهد. به دلیل حرارت بالای ایجاد شده در زمان جوشکاری، گاز محافظ به تنهایی قادر به خنک کردن مشعل نیست از این رو از آب به عنوان خنک کننده استفاده می شود. تورچ یا مشعل ها از دسته، بدنه، نازل، کوپلینگ و سوپاپ جریان گاز ساخته شده اند.
کابل اتصال
کابل اتصال یا کابل جوشکاری عنصری حیاتی و اساسی در فرایند جوشکاری است. این کابل وظیفه انتقال جریان الکتریکی قوی از منبع تغذیه به دستگاه جوش آرگون و در نهایت به محل جوش را بر عهده دارد. بدون وجود کابل اتصال، انجام هیچ گونه عملیات جوشکاری امکان پذیر نخواهد بود.
کابل اتصال به عنوان یک هادی، جریان الکتریکی با شدت بالا را از منبع تغذیه به محل جوش منتقل می کند. عایق مناسب کابل، از بروز خطر برق گرفتگی جلوگیری و ایمنی جوشکار را تضمین می کند. از طرف دیگر کابل با کیفیت، جریان پایدار و یکنواختی را فراهم کرده و به ایجاد قوس الکتریکی پایدار کمک می کند.
الکترود تنگستن
ماده مورد نیاز برای شروع عملیات جوشکاری، الکترود تنگستن است. الکترود تنگستن در گروه الکترودهای ذوب نشدنی مطابق با استاندارد AWS A5.12 قرار می گیرد. الکترود تنگستن در اندازه ها و گونه های متنوع تولید شده و مورد استفاده قرار می گیرد. الکترود خالص، توریم دار و زیر کونیوم دار که هر کدام با توجه به قابلیت هایی که دارند مورد استفاده قرار می گیرند.
الکترود تنگستن خالص نسبت به سایرین ارزان تر، ظرفیت حمل الکتریسیته کمتر، قابل استفاده با جریان برق متناوب یا AC و با طول عمر کوتاه است. الکترود توریم دار، با ظرفیت حمل الکتریسیته بالاتر دارای طول عمر بیشتری است. این نوع الکترود با جریان DC یا مستقیم کار می کند. الکترود زیرکونیوم دار از بهترین نوع الکترود در جوشکاری آلومینیوم و منیزیم است. این نوع الکترود تمامی قابلیت های دو الکترود قبلی را دارد.
دسته بندی الکترود تنگستن بر اساس رنگ ها انجام می شود. انتخاب الکترود تنگستن مناسب بر اساس قطر آن در جوشکاری، شدت جریان و نوع جریان برق ورودی (مستقیم یا متناوب) بستگی دارد.
سیم جوش
سیم جوش ها بر اساس استاندارد AWS طبقه بندی می شوند. سیم جوش یا فیلر جوشکاری با هدف ایجاد اتصال بین دو سطح جدا شده در بیشتر فعالیت های جوشکاری کاربرد دارد. طول این سیم ها بین 61 تا 91 سانتیمتر است و به صورت کلاف شده عرضه می گردد. انتخاب الکترود مناسب به نوع فلز، ضخامت قطعه کار و نوع جریان بستگی دارد.
انبر اتصال
ثابت نگه داشتن قطعه کار در حین جوشکاری بر عهده انبر اتصال است. انبرهای مختلفی با گیره های متفاوت، برای قطعات با شکل های مختلف وجود دارند.
انبر جوش
انبر جوش یکی از ابزارهای اساسی و ضروری در فرایند جوشکاری است. این ابزار با طراحی خاص خود، وظیفه نگه داشتن الکترود جوشکاری و ایجاد یک اتصال الکتریکی قوی و پایدار بین کابل جوشکاری و الکترود را بر عهده دارد. به عبارت ساده تر، انبر جوش مانند یک گیره عمل می کند که الکترود را محکم در جای خود نگه داشته و امکان ایجاد قوس الکتریکی و ذوب فلز را فراهم می کند.
انبر جوش با طراحی آرواره های خود، الکترود را محکم گرفته و از حرکت آن در حین جوشکاری جلوگیری می کند. قسمت فلزی انبر جوش به کابل جوشکاری متصل می شود و جریان الکتریکی را به الکترود منتقل می کند. این اتصال باید محکم و بدون مقاومت باشد تا از ایجاد جرقه های اضافی و کاهش کیفیت جوش جلوگیری شود. برخی از انواع انبرهای جوش، دارای مکانیزمی هستند که به جوشکار اجازه می دهد جریان الکتریکی را بهتر کنترل کند.
استفاده از انبر جوش باعث می شود که جوشکار در تماس مستقیم با قسمت های داغ جوشکاری قرار نگیرد و خطر سوختگی کاهش یابد. همچنین یک انبر جوش خوب باعث می شود که قوس الکتریکی پایدار و یکنواخت باشد و در نتیجه، جوش با کیفیت تری تولید شود.

کاربرد جوشکاری آرگون
جوشکاری آرگون یکی از مهم ترین روش های جوشکاری در صنایع مختلف است. کاربرد این شیوه در صنایع نظامی، دریایی، پتروشیمی، هوایی، نیروگاه های برق و… بیشتر به چشم می خورد. فرآیند این نوع جوشکاری با هدف اتصال فلزات سخت و غیر سخت، آهنی و غیر آهنی به یکدیگر انجام می شود.
جوشکاری آرگون برای تمامی فلزات در هر ضخامتی کاربرد دارد. علاوه بر این، جوشکاری صفحات نازک و باریک مانند آلومینیوم و لوله های تحت فشار را نیز پوشش می دهد.
برخی از کاربردهای جوشکاری آرگون عبارتند از:
- جوشکاری فلزات حساس مانند آلومینیوم، تیتانیوم، زیرکونیوم و منیزیم
- جوشکاری صفحات نازک به دلیل دقت بالا
- جوشکاری قطعات کوچک به دلیل انعطاف پذیری بالا
- جوشکاری قطعات حساس به دلیل کیفیت جوش مناسب
برخی از صنایعی که از جوشکاری آرگون استفاده می کنند عبارتند از:
- صنایع هوا و فضا برای ساخت و تعمیر هواپیماها، فضاپیماها و موشک ها
- صنایع خودروسازی برای ساخت و تعمیر بدنه خودروها
- صنایع پزشکی برای ساخت و تعمیر تجهیزات پزشکی
- صنایع غذایی ساخت و تعمیر تجهیزات غذایی
- صنایع الکترونیک برای ساخت و تعمیر قطعات الکترونیکی
مزایا و معایب جوشکاری آرگون
اجرای عملیات جوشکاری آرگون با توجه به استفاده از ابزار و دستگاه های پیشرفته، مزیت هایی به همراه داشته که امروزه بیشترین کاربرد را در صنایع کوچک و بزرگ دارد.
- اجرای جوشکاری دقیق، تمیز، بدون کجی سطوح با سرعت پایین
- قابلیت جوشکاری طولانی مدت
- اتصال فلزات نازک و ظریف با کیفیت و دقت بالا
- عدم ایجاد جرقه و دود در حین کار
- قابلیت اتصال فلزات در هر وضعیتی (صاف یا قوسی)
- کاربرد مناسب در اتصالات ظریف برای کارهای زینتی
در کنار تمامی مزیت های استفاده از جوشکاری آرگون می توان به برخی از معایب آنها نیز اشاره کرد.
- عوارض ناشی از حرارت و گرمای بالا مانند گرمازدگی، خستگی، تهوع و درد شکم
- پیدایش بیماری های چشمی در صورت عدم استفاده از ماسک مخصوص
- تولید اشعه مادون قرمز و پیدایش بیماری های پوستی
- ایجاد پیری زودرس در فرد جوشکار
جوشکاری آرگون به عنوان یکی از انواع روش های جوشکاری و برقراری اتصال بین فلزات است. این شیوه با کمک گاز آرگون به عنوان محافظ و خنک کننده تورچ یا مشعل در حین جوشکاری عمل می کند. اجرای این عملیات باید در فضای ایمن و با استفاده از تجهیزات ایمنی مانند کفش، عینک، ماسک و لباس مخصوص جوشکاری آرگون انجام شود تا از فرد جوشکار در برابر خطرات جوشکاری آرگون محافظت شود.
برای اجرای این کار علاوه بر داشتن تجهیزات جوشکاری TIG، به نیروی کار آزموده با تجربه کار کافی نیاز است. در صورت فراهم نمودن تمامی ابزار مورد نیاز می توان یک جوشکاری بی نقص و ایمن را اجرا نمود.
سلام امکان جوش آرگون در محل ترکیدگی جای پیچ سیلندر که به اشتباه بسته شده و فشار به سیلندر وارد شده و از همین نقطه ترکیده است،وجود دارد متاسفانه با بسته شدن در اثر غفلتکاری پیچ بدون بوش بسته شده و سیلندر ترکیده و اب روغن قاطی کرده. خواستم ببینم با توجه به اینکه تقریبا محل جوش، بد جا هست، آیا این کار امکان پذیر است و دوم چقدر میتواند در دمای بالای موتور دوام بیاره ممنونم اگر دوستان راهنمایی بفرمایند