همه چیز را درباره انواع کوره در تولید آهن آلات بدانید!
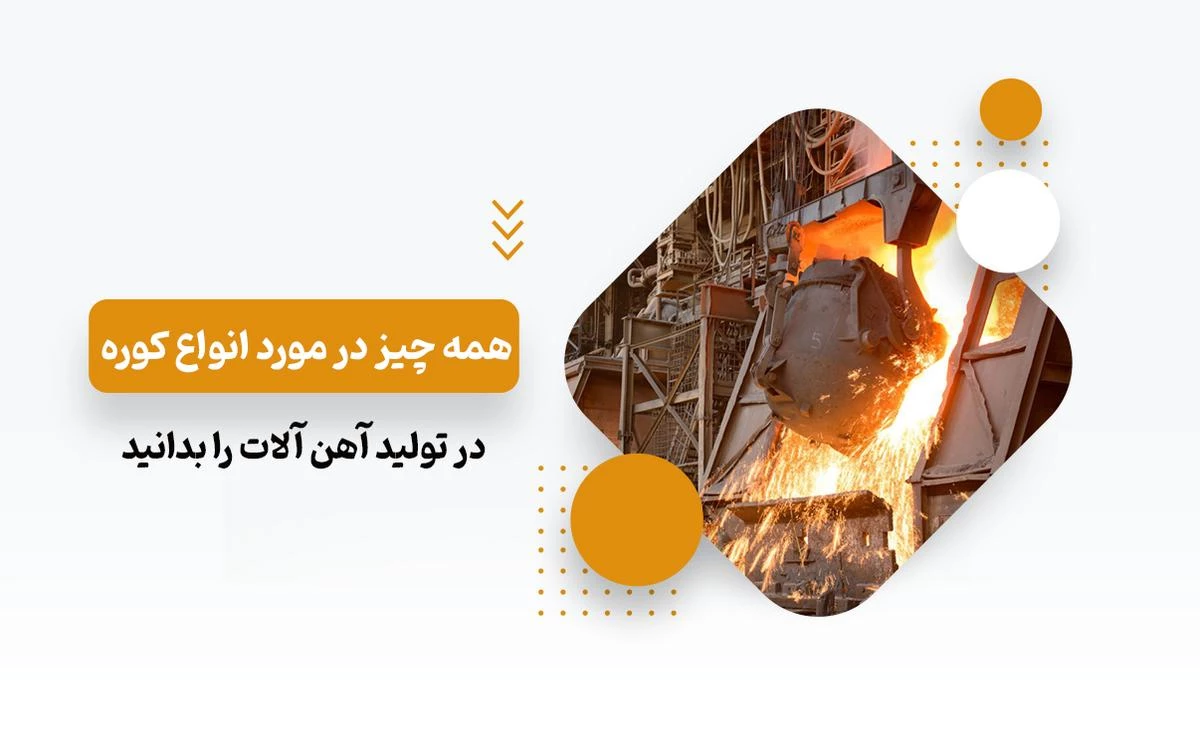
دسترسی سریع به محتوای این مطلب
کارخانه ها برای تولید آهن آلات و مقاطع فلزی، از روش ها و ابزار آلات مختلفی استفاده می کنند. در این بین روش ذوب از مرسوم ترین راهکارهایی است که برای تولید آهن آلاتی مانند تیرآهن، میلگرد و… استفاده می شود. لازم به ذکر است انتخاب شیوه نورد سرد یا گرم، بر قیمت میلگرد و سایر محصولات فولادی نقش موثری دارد.
کوره یکی از ملزومات موردنیاز برای عملیات ذوب است. در دنیای امروز کوره های مختلفی با ویژگی های منحصر به فرد در صنایع فولادی و فلزی، مورد استفاده قرار می گیرند. به همین دلیل در این مقاله، در مورد انواع کوره در تولید آهن آلات صحبت می کنیم.
کاربرد کوره های ریخته گری
کوره ها در ایجاد خصوصیات مواد و کیفیت نهایی محصولات، نقس بسیار موثری را ایفا می کنند. انواع مختلفی از کوره در مراحل مختلف تولید مقاطع فولادی، استفاده می شوند. از این دستگاه ها در مرحله پیشگرمایش میله، تولید محصولات آهنی و غیر آهنی مانند ذوب قراضه ها، ایجاد تغییر شکل در صفحات فلزی به شیوه گرمایشی و هم چنین عملیات حرارتی فولادی استفاده می شود.
برخی از کاربردهای رایج کوره های ریخته گری عبارتند از:
- تولید فولاد و آهن برای استفاده در سازه ها، وسایل نقلیه، ماشین آلات و سایر محصولات
- تولید آلومینیوم، مس و سایر فلزات غیر آهنی برای استفاده در قطعات الکترونیکی، لوله ها، کابل ها و سایر محصولات
- تولید آلیاژهای خاص برای استفاده در کاربردهای تخصصی مانند قطعات موتور، ابزار و جواهرات
انواع کوره در تولید آهن آلات
کوره ها انواع مختلفی مانند کوره بوته ای، کوره القایی، کوره کوپلا، کوره مقاومتی الکتریکی، کوره قوس الکتریکی و کوره شعله ای می شوند. این دستگاه ها کاربردها، مزایا و معایب بسیاری دارند که آنها را از یکدیگر متمایز می کند. در ادامه بیشتر به معرفی آنها می پردازیم.
- کوره بوته ای
- کوره القایی
- کوره کوپلا
- کوره مقاومتی الکتریکی
- کوره قوس الکتریکی
- کوره شعله ای
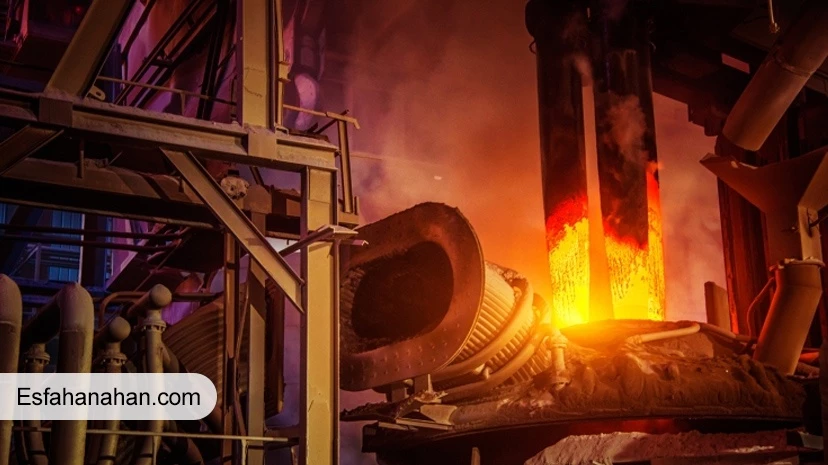
1) کوره بوته ای
کوره بوته ای از قدیمی ترین کوره هایی است که اغلب در کارگاه های ریخته گری، استفاده می شود. با پیشرفت تکنولوژی و وارد شدن فناوری به سیستم تولید، همچنان استفاده از کوره بوته ای رایج بوده و امروزه در برخی کارگاه ها نیز از آن استفاده می شود.
در کوره بوته ای بدون ایجاد تماس میان مواد اولیه و سوخت، مواد مذاب را از وارد کردن حرارت به مواد اولیه تولید می کنند. از جمله مواد سوختی که در این کوره استفاده می شوند گازوئیل، مازوت، گاز طبیعی و الکتریسیته هستند. این کوره ها ساده ترین نوع کوره های ریخته گری هستند و از یک ظرف نسوز، برای ذوب فلز استفاده می کنند. کوره های بوته ای برای ذوب فلزات با نقطه ذوب پایین مانند آلومینیوم و منیزیم مناسب هستند.
کاربرد و مزایای کوره بوته ای
کوره بوته ای در آلیاژهایی با نقطه ذوب پایین یا آلیاژهایی که میل کمتری برای ترکیب شدن با اکسیژن را دارند (مانند منیزیم)، استفاده می شوند. این دستگاه به دو دسته کوره ثابت و بوته متحرک با گردان، تقسیم بندی می شود. سهولت ساخت، مقرون به صرفه بودن و کیفیت محصول مذاب تولید شده، از جمله مزیت های این نوع کوره هاست که باعث افزایش کاربرد آنها در کارگاه های کوچک می شود.
2) کوره کوپلا
ساختار کوره کوپلا به صورت استوانه فولادی است که اغلب در ذوب کردن چدن کاربرد دارد. ساختمان این کوره با جداره نسوز پوشانده شده و اندازه دهانه یا قطر این استوانه فولادی، بر اساس میزان ظرفیت و سرعت ذوب مواد تغییر می کند. از جمله محصولاتی که با استفاده از این کوره به دست می آیند پیش گرم کن هوا، ریل شارژ و محل تصفیه گاز هستند. این نوع از کوره تولید آهن آلات، ظرفیت ذوب 100 تا ده ها تن محصول نهایی را دارد.
مزایای کوره کوپلا
سهولت استفاده از کوره کوپلا و تولید مواد مذاب در حجم بالا، از جمله مزیت هایی است که برای این نوع کوره وجود دارد. در مقابل استفاده از کوره کوپلا به دلیل تولید فوق گدازه های بالا و انعطاف پذیری پایین، توصیه نمی شود.
3) کوره مقاومت الکتریکی
وجود المنت ها و عبور جریان الکتریکی از آنها موجب شده تا حرارت مورد نیاز برای مذاب کردن مواد اولیه در کوره های مقاومت الکتریکی فراهم شود. در ساخت المنت ها از مواد آلیاژی با نقطه ذوب بالا، مقاوم در برابر خوردگی و اکسید شدن استفاده می شود تا در حرارت های بالا ذوب نشوند. کوره مقاومت الکتریکی در دو نوع گرم کننده مستقیم و غیرمستقیم تولید و به کار برده می شوند.
گرم کننده مستقیم: در این نوع کوره مقاومت الکتریکی، جریان برق با عبور از یک ترانسفرمر ولتاژ پایین از خلال شارژ یا فولادی که ذوب مشده، موجب گرم شدن شارژ می شود. این روش تنها با هدف گرم نمودن (نه ذوب کردن آهن آلات) استفاده می شود.
گرم کننده غیر مستقیم: این نوع از کوره با عبور جریان الکتریکی از المنت های پیچیده شده اطراف کوره، حرارت را وارد کوره و سپس به بوته انتقال می دهد. این کوره، به منظور اجرایی نمودن عملیات حرارتی و ذوب آهن آلات به کار برده می شود.
مزایای کوره مقاومت الکتریکی
از این نوع کوره، به همراه کنترل ترکیب شیمیایی مواد مذاب استفاده می شود. اما همانند کوره های مقاومتی به دلیل استفاده از جریان الکتریکی، هزینه های مصرفی بالایی دارد. علاوه بر این، ظرفیت تولید این نوع کوره ها حداکثر 500 کیلوگرم است که چندان مقدار قابل توجهی نیست.
4) کوره ذوب آهن القایی
یکی از انواع کوره های جدید و مدرن که با استفاده از عبور جریان الکتریکی باعث ذوب مواد اولیه می شوند، کوره القایی است. این کوره در دسته کوره های مقاومتی قرار می گیرد . این دستگاه، جریان الکتریکی لازم برای یک میدان مغناطیسی در سیم پیچ را ایجاد می کند که با تولید جریان های گردابی در فلز، موجب ذوب شدن آن می شود. فرکانس های این کوره در سه دسته پایین 50 هرتز، متوسط بین 200 تا 1000 هرتز و فرکانس بالای 1000 هرتز به بالا تقسیم بندی می شوند.
کوره القایی فرکانس پایین: کوره القایی فرکانس پایین شامل یک سیم پیچ ثانویه و سیم پیچ دارای هسته فولادی است که عملکردی مشابه با ترانسفورمر دارد.
کوره القایی فرکانس متوسط و بالا: در این دو نوع کوره، جریان برق توسط فرکانس های شبکه و دستگاه های تبدیل کننده از سیم پیچ های تعبیه شده در اطراف بوته، عبور کرده و موجب ذوب شارژ می شود.
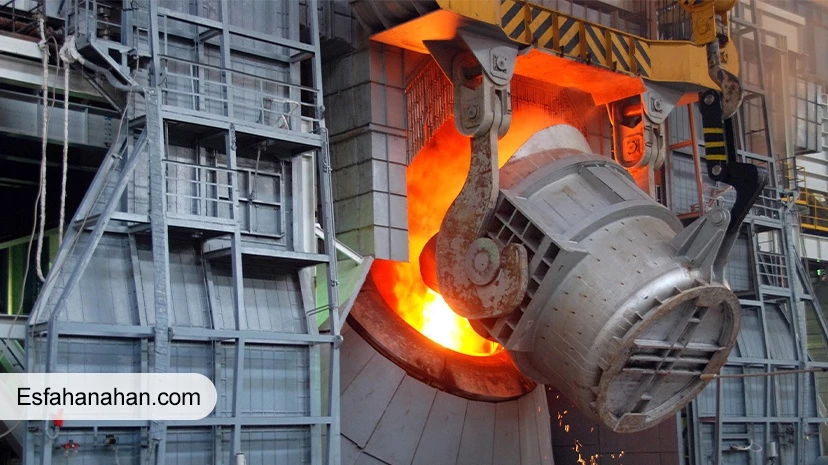
کاربرد کوره القایی
کوره القایی با فرکانس و راندمان پایینی که دارد، به عنوان نگه دارنده مورد استفاده قرار می گیرد. توصیه می کنیم از این فرکانس کوره القایی برای ذوب مواد استفاده نشود. کوره هایی با فرکانس های بالا، در آزمایشگاه ها برای ذوب مواد استفاده می شوند. استفاده از کوره های القایی باعث شده تا حرارت به صورت یکسان توزیع شده و در نتیجه مقدار انرژی کمتری مصرف شود. همچنین ترکیبات شیمیایی قابل کنترل هستند و با محدودیت افزایش دما روبرو نمی شوید.
در مقابل تمامی مزیت های کوره القایی، استفاده از جریان الکتریکی باعث افزایش هزینه ها شده و هم چنین امکان تصفیه مواد مذاب شده، از یکدیگر وجود ندارد و به همین دلیل باید قبل از استفاده تمیز شوند.
5) کوره قوس الکتریکی
کوره قوس الکتریکی یکی از انواع کوره های الکتریکی است، که در صنعت مورد استفاده قرار می گیرد. در این نوع کوره یک فضای بزرگ، با بدنه فولادی پوشانده شده از مواد نسوز و لوله های آبگرد وجود دارد که مواد اولیه با قرار گرفتن در معرض حرارت به صورت مذاب در می آیند.
استفاده از لوله های آبگرد، به دلیل از بین نرفتن ماده نسوز در برابر دمای بالاست. کوره قوس الکتریکی نیز به دو دسته قوس الکتریکی مستقیم و غیرمستقیم تقسیم بندی می شود.
قوس الکتریکی مستقیم: در قوس الکتریکی مستقیم، مواد اولیه ای مانند فولاد و چدن، حرارت دیده و به صورت مذاب در می آیند. در این نوع کوره، حرارت در قوس الکتریکی در میان شارژ به صورت مستقیم جریان پیدا کرده و باعث می شود تا مواد ذوب شوند. در این نوع می توان با قرار دادن یک الکترود در بالا و یکی در پایین شارژ، یک قوس الکتریکی بین دو الکترود ایجاد کرد.
در برخی موارد قوس الکتریکی، مستقیم از یک کاتد گرافیتی تولید و ضمن دریافت حرارت از قوس، آن را به آند انتقال می دهد و در این حالت آند به عنوان شارژ کوره، وظیفه انتقال حرارت را بر عهده می گیرد.
قوس الکتریکی غیرمستقیم: در قوس الکتریکی غیرمستقیم، آلیاژهایی مانند مس به صورت مذاب تولید می شوند. در این نوع کوره یک قوس الکتریکی مابین دو یا چند الکترود ایجاد می شود. این قوس در بالای شارژ، درون کوره قرار داشته و از طریق حرارت ایجاد و به شارژ انتقال داده شده و باعث ذوب مواد می شود.
میزان ظرفیت تولید کوره قوس الکتریکی، 180 تا 200 تن مواد مذاب است. یکی از کاربردهای کوره های قوس الکتریکی در صنعت، تغییر ولتاژ ثانویه است. در حالت کلی کوره قوس الکتریکی در سه نوع تک فاز، دو فاز و سه فاز تولید و به کار گرفته می شود. از قوس الکتریکی ترانس سه فاز، برای دریافت انرژی مورد نیاز کوره از جریان برق با ولتاژ مناسب استفاده می شود.
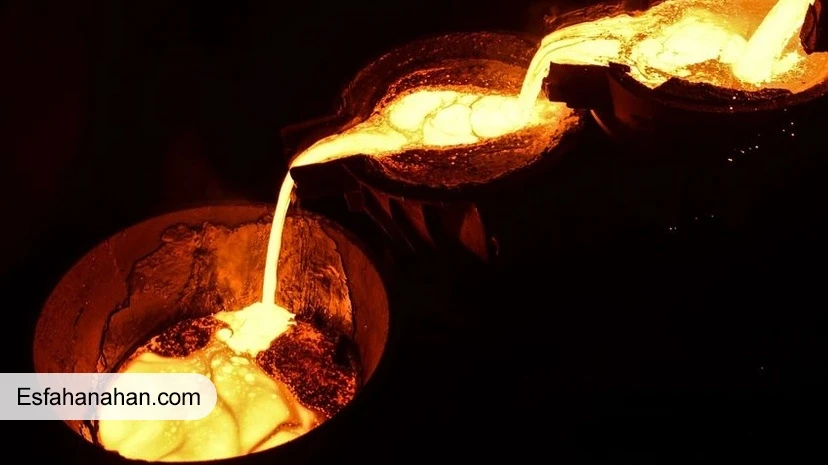
مزایای کوره قوس الکتریکی
مزیت های کوره قوس الکتریکی موجب شده، تا کاربرد بیشتری نسبت به سایرین داشته باشد. از جمله مزیت های این دستگاه می توان به ظرفیت، قدرت تولید بالا، دوام، استحکام بالا، استفاده از قراضه های ارزان به عنوان ماده اولیه، تولید دما، حرارت بالا و… اشاره کرد. در مقابل تمام مزایای این نوع کوره همانند سایر کوره های الکتریکی مقدار هزینه مصرفی بالا موجب می شود تا هزینه نهایی پروژه نیز افزایش یابد.
6) کوره شعله ای
شاید برایتان جالب باشد که تولید آهن آلات توسط کوره ها در قرون وسطی با استفاده از کوره های شعله ای به منظور ریخته گری زنگ های کلیسا صورت می گرفت. در این نوع کوره ها، مواد شارژ با مواد سوختی در تماس مستقیم هستند و در اثر وارد شدن حرارت، ذوب می شوند.
سوخت مورد استفاده در این نوع کوره ها گازوئیل یا گاز طبیعی است. شارژ نمودن کوره ها از طریق درب و سقف کوره انجام می شود. میزان تولید کوره شعله ای برای آلیاژهای غیر آهنی به اندازه 15 تا 75 تن است. شکل ظاهری این نوع کوره بهصورت مکعب مستطیل یا استوانه ای است.
مزایای کوره شعله ای
سهولت ساخت، حجم تولید مواد ذوب بالا، سرعت بالای ذوب و عدم نیاز به سرمایه گذاری و صرف هزینه های گزاف برای تولید این کوره ها از مزایای کوره شعله ای به شمار می روند. در مقابل به دلیل پایین بودن درجه حرارت، نمی تواند راندمان بالایی داشته باشد.
آهن آلات یکی از ملزومات مصرفی، در صنایع مختلف هستند. شیوه های مختلفی به منظور تولید آهن آلات با استفاده از تجهیزات و دستگاه های متفاوت وجود دارند. استفاده از کوره ها با هدف حرارت دادن و تولید مواد مذاب و ساخت آهن آلات، یکی از روش های مدرنی است که برای تولید مقاطع فولادی استفاده می شود.
برای تولید آهن آلات از انواع کوره استفاده می کنند که هرکدام دارای ویژگی های منحصر بهفرد خود هستند و برای تولید محصولات متفاوت مورد استفاده قرار می گیرند. نظر شما در مورد این روش تولیدی چیست؟ با ما درمیان بگذارید.
چه کوره هایی برای تولید محصولات فولادی استفاده می شود؟
کوره های بوته ای، کوره القایی، کوپلا، مقاومتی الکتریکی و همچنین قوس الکتریکی، متداول ترین کوره ها برای تولید فولاد هستند.
مزایای استفاده از کوره قوس الکتریکی چیست؟
ظرفیت و قدرت تولید بالا، دوام و استحکام زیاد، استفاده از قراضه های ارزان به عنوان ماده اولیه و همچنین تولید دما و حرارت بالاتر، از مزایای این نوع کوره هستند.
کوره ها به چند دسته تقسیم می شوند؟
کوره ها به دسته های کوره کوپلا، کوره بوته ای، کوره مقاومت الکتریکی و… تقسیم می شوند.
اوکی ولی عکس از مدل های مختلف نداشت و این بَده