آهن اسفنجی چیست و چه کاربردی در ریخته گری دارد؟
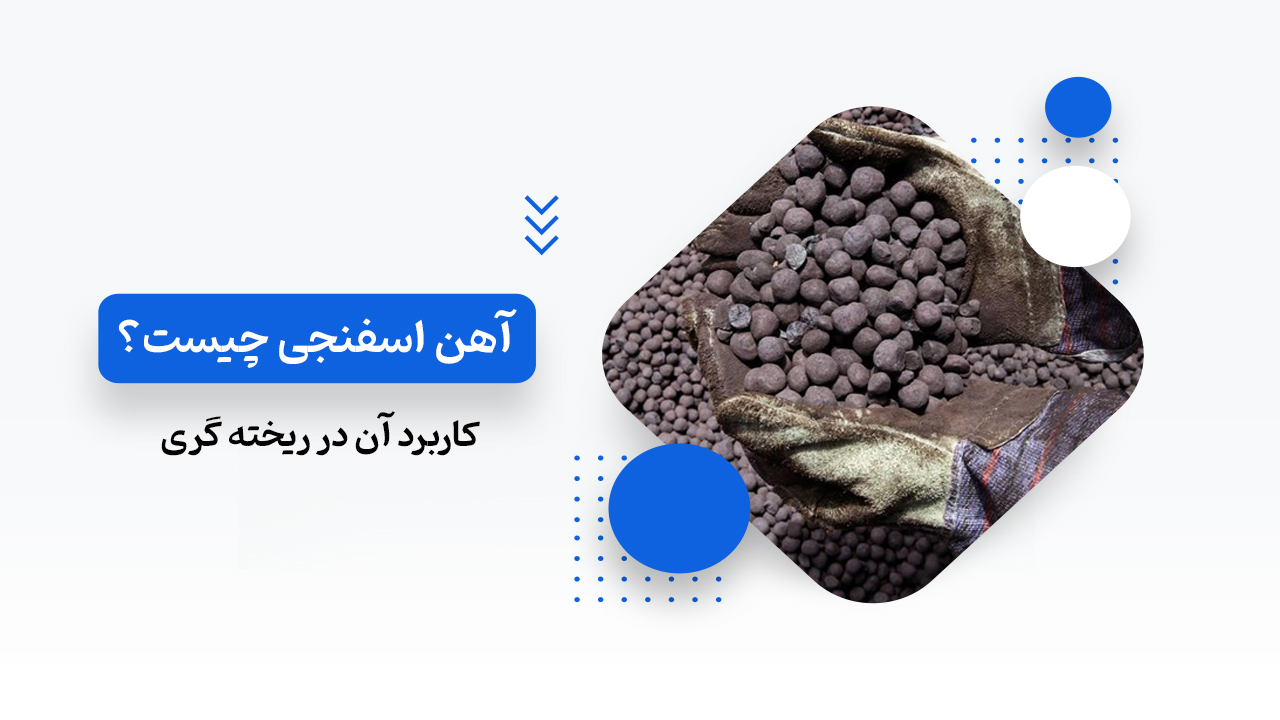
دسترسی سریع به محتوای این مطلب
آهن اسفنجی از احیای مستقیم سنگ آهن به دست آمده و طی عملیات احیای بی واسطه، بدون نیاز به ذوب سنگ آهن، اکسیژن آن حذف می شود. در این روش، گندله سنگ آهن با عیار ۶۷%، احیا شده و گندله متخلخل تشکیل می شود. این محصول پس از ذوب و احیا در فولادسازی، در فرآیند ریخته گری به شکل محصولات مورد نیاز در می آید و به سه شکل اسلب (تختال)، بیلت (شمش) و میلگرد مورد استفاده قرار می گیرد.
در این مطلب از دانشنامه اصفهان آهن قصد داریم به بررسی مشخصات، ویژگی ها و کاربرد آهن اسفنجی در صنایع بپردازیم. پس با ادامه مطلب همراه باشید.
دلایل استفاده از گندله متخلخل
شکل ظاهری این محصول به صورت قطعات کروی شکل (گندله) است که به دلیل متخلخل بودن ساختار آن، ظاهر اسفنجی دارد؛ به همین دلیل به آن آهن اسفنجی می گویند. این محصول دارای عیار بالای آهن بوده که امروزه با توجه به کمبود ضایعات اهن، افزایش قیمت آن و مشکلات زیست محیطی مورد توجه قرار می گیرد.
حدود ۵% از فولاد جهان، از این محصول (DRI) تولید می شود و روند رو به افزایشی دارد. این محصول، از احیای مستقیم سنگ آهن بدست آمده و اصطلاحاً به آن DRI نیز می گویند. امروزه گندله متخلخل با کاهش سنگ آهن بدون ذوب کردن آن ایجاد می شود و همین موضوع باعث شده که یک منبع انرژی کارآمد برای سازندگان فولاد باشد.
تاریخچه آهن اسفنجی
استفاده از گندله متخلخل، حدوداً از سال ۸۹ در کوره های القایی ایران شروع شد. در آن سال ها کمبود قراضه احساس نمی شد و هر چند روند کیفیت قراضه نزولی بود ولی باز هم کسی به فکر استفاده از آن نبود. هندی ها و چینی هایی که کوره القایی به ایران فروخته بودند هم تشویق به استفاده از آن نمی کردند. شاید به خاطر اینکه پارامترهای مربوط به راندمان کوره هایشان افت می کرد.
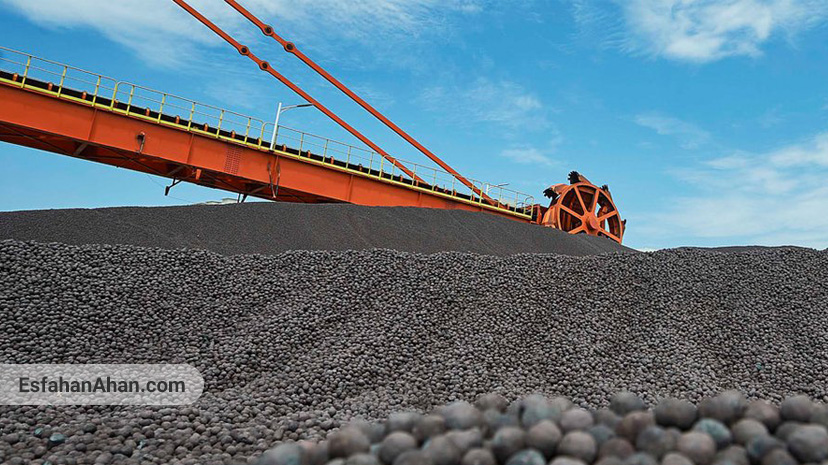
در سال ۸۹، یکی از کارخانه های القایی یزد به دلایلی برای اولین بار به مصرف اسفنجی رو آورد. بسیاری از کارخانه ها، البته با تأخیر، از این محصول استفاده می کردند. اولین واکنش، تقریباً در تمامی کارخانه ها، منفی بود. زیرا اولاً با روش شارژ آن آشنا نبودند و ثانیاً فسفر و گوگرد آن در مقایسه با قراضه، آنالیز ذوب را به هم می زد و کربن بالای آن کار را سخت می کرد. همچنین زمان ذوب طولانی می شد و سرباره بسیار، وحشتناک بود. لذا به محض استفاده، بسیاری از کارخانه ها استفاده از آن را تا همین اواخر متوقف کردند.
اما امروزه بسیاری از واحدهای کوچک و بزرگ تولید فولاد در کشور، از این روش ها استفاده می کنند. ایران منابع طبیعی در دسترس تری برای احیای مستقیم دارد. گندله متخلخل جایگزین مناسبی برای ضایعات آهن است. بنابراین می توانیم درصد بالایی از مواد اولیه جهت تأمین ذوب مورد نیاز واحدهای فولادسازی را بجای استفاده از ضایعات، از طریق این محصول تأمین کنیم.
کاربردهای مهم آهن اسفنجی در ریخته گری
از اهن اسفنجی در ریخته گری فولاد هم استفاده می شود. این محصول نسبت به آهن، عیار بالاتری دارد و به این دلیل که در ایران منابع مختلفی برای استخراج و احیای آهنگری وجود دارد، از آن در تولید فولاد استفاده می شود. در اصل گندله متخلخل، ماده اولیه تولید فولاد در ریختهگری است که ذوب می شود و به کمک آن می توان فولاد را تولید کرد.
قبل از تولید آهن اسفنجی، از ضایعات و قراضه ها در ریخته گری فولاد استفاده می شد اما امروزه با وجود آهن اسفنجی، فولاد حاصل شده کیفیت و عیار بالایی دارد و استحکام و مقاومت آن بالاست.
این نکته را هم اضافه کنیم که در زمان تولید آهن اسفنجی، حدود 5 درصد از مواد اولیه آن به نرمه آهن اسفنجی تبدیل می شوند که از آن می توان برای کاربردهای مختلفی استفاده کرد. کاربرد این محصول با خود آهن اسفنجی متفاوت است و در اکثر موارد می توان از آن برای ماده اولیه در تولید بریکت آهن استفاده کرد.
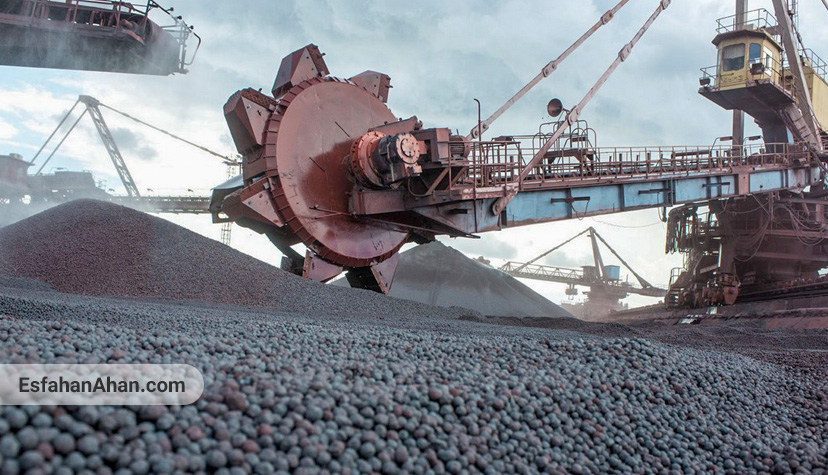
با وجود آنکه بیش تر تولید فولاد خام در جهان به وسیله روش کوره بلند تولید می شود، اما موارد ذیل، استفاده از روش احیای مستقیم و کوره های الکتریکی را، مخصوصاً در ایران، توجیه پذیرتر می کنند:
- با توجه به استفاده از قراضه آهن، این روش سریع تر است.
- هزینه راه اندازی یک واحد کوره بلند نسبت به یک واحد احیای مستقیم و کوره الکتریکی در ظرفیت های متناظر، بالاتر است.
- روش کوره بلند محدودیت های زیست محیطی بیشتری نسبت به روش احیای مستقیم دارد.
- آهن اسفنجی عیار بالاتری نسبت به آهن خام دارد.
- کوره بلند در ظرفیت های بالا (حداقل یک و نیم میلیون تن در سال) دارای توجیه اقتصادی بیشتری است، در حالی که از روش احیای مستقیم می توان در واحد های کوچک فولادسازی نیز با توجیه اقتصادی مناسب استفاده کرد.
- آهن اسفنجی را می توان به صورت آهن گرم کلوخه شده (HBI) در آورد و به سهولت حمل یا ذخیره کرد. در صورتی که حمل آگلومره که خوراک کوره بلند است سخت تر به نظر می رسد.
- در فرایند احیای مستقیم م یتوان از گاز طبیعی بدون حذف ناخالصی ها استفاده کرد.
- در عین حال شرکت های ذوبآهن اصفهان، فولاد میبد، فولاد زاگرس ذوب آهن غرب کشور و فولاد زرند، در مجموع حدود ۵ میلیون تن فولاد، از طریق روش کوره بلند تولید خواهند کرد که با توجه به پتانسیل های موجود در کشور، به نظر کافی می آیند.
علاوه بر این، حتی از آن، به دلیل کمبود قراضه و ضایعات فلزی، می توان در کوره القایی نیز استفاده کرد.
روش های تولید آهن اسفنجی با استفاده از منابع گازی و زغال سنگ
تولیدگندله متخلخل از سنگ آهن، عموماً به دو روش گازی (Gas Based) یا استفاده از زغال سنگ (Coal Based) انجام می شود. معمولاً در کشورهایی که دارای ذخایر گاز هستند، از روش گازی بیشتر استفاده می شود. در ایران نیز به طور مثال، فولاد خوزستان فولاد مبارکه از گاز به عنوان ماده احیا کننده استفاده می کند.
برای تولید آهن اسفنجی با استفاده از گاز طبیعی از فناوری های زیر استفاده می شود:
• میدرکس
• HYL
• Purofer
شناخته شده ترین روش های احیای مستقیم گازی، روش های میدرکس و HYL هستند. همچنین شرکت ایریتک و MMTE دارای لیسانس ساخت کارخانه های احیای مستقیم (از کوبه استیل ژاپن) با تکنولوژی میدرکس هستند (میدرکس تکنولوژی اصالتاً آمریکایی است).
منابع زغال سنگ عبارتند از:
- SL/RN (اس – آل – آر – ان)
- Jindal (جیندال)
- DRC (دی – آر – سی)
تولید آهن اسفنجی به روش میدرکس
این روش به عنوان پر استفاده ترین روش های تولید آهن اسفنجی در ایران و جهان شناخته شده است. در این روش، گاز طبیعی وارد واحد شکست گاز می شود، سپس بر اثر حرارت وارد شده و کتالیست های مخصوص، به هیدروژن و کربن تبدیل می شود. سپس این هیدروژن و کربن، در کوره ای که کوره احیا نام دارد، وارد شده و با اکسیژن گندله سنگ آهن ترکیب می شود و باعث احیای سنگ آهن خواهد شد.
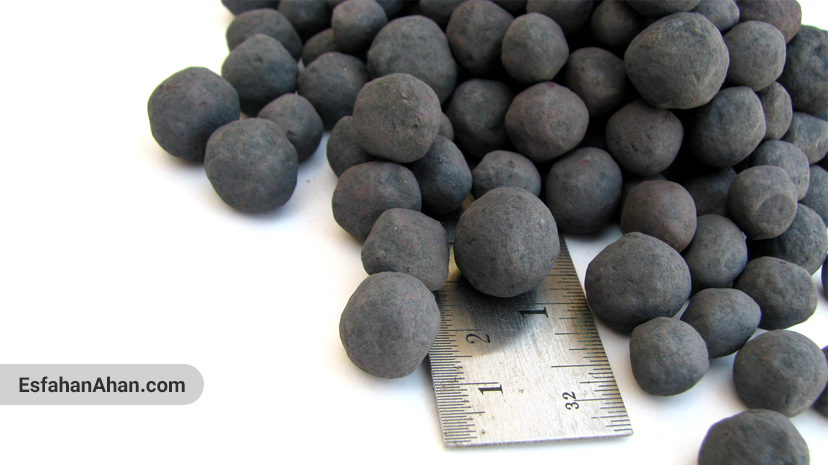
این روش به عنوان کم مصرف ترین و پر بازده ترین روش ها در ایران و جهان شناخته می شود. حدود 80 درصد از آهن اسفنجی ایران، به این روش تولید شده است.
تولید آهن اسفنجی به روش HYL
بعد از روش میدرکس، روش HYL معروف ترین راه تولید است اما مصرف برق بالا و مشکلات ظرفیتی دارد. بنابراین روش HYL و روش هایی که بر مبنای زغال سنگ هستند، در ایران استفاده نمی شوند.
ترکیبات شیمیایی تولید آهن اسفنجی به روش میدرکس در جدول زیر آورده شده است:
Production Range | Component |
86-85.9% | Fe (total) |
Min 90% | Fe (metallization) |
78.5-82% | Fe (metal) |
1.3-2% | C |
Max 0.01% | S |
Max 0.1% | P |
Max 5.5% | SiO2 |
Max 1% | Al2O3 |
Max 1.1% | CaO |
Max 2.5% | MgO |
1.6-1.9 tons/m3 | Bulk Density |
آمار و اطلاعات مهم درباره آهن اسفنجی
تولید فولاد از طریق احیای مستقیم و کوره های الکتریکی در راستای سیاست های شرکت ملی فولاد و وزارت صنایع نیز بوده است. بر این اساس، با استفاده از آمار، به بررسی وضعیت آهن اسفنجی در جهان و کشورهای پیش رو در این زمینه می پردازیم.
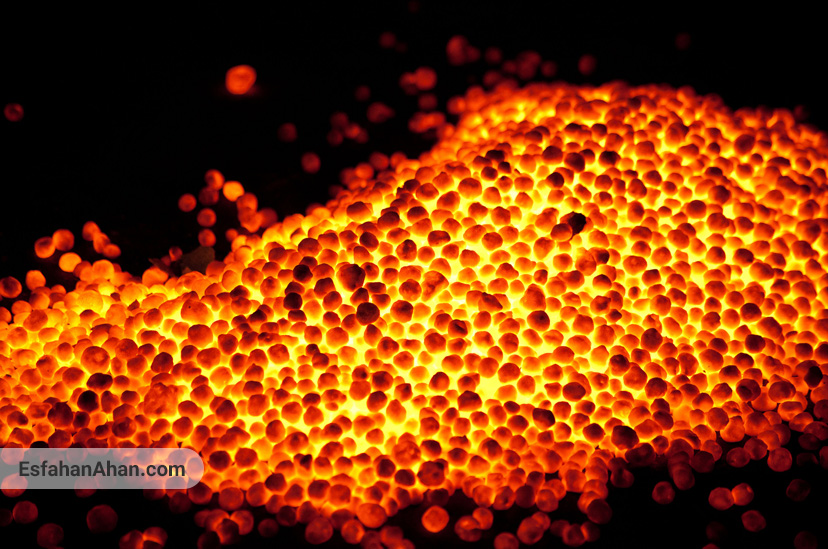
- بر اساس اطلاعات، هندوستان بزرگ ترین تولید کننده آهن اسفنجی در دنیا است. این کشور از مجموع تولید۹/۶۴ میلیون تن آهن اسفنجی دنیا در سال ۲۰۰۷، حدود ۱/۱۸ میلیون تن یعنی حدود ۲۸ درصد از کل تولید را به خود اختصاص داده است.
- حدود ۸۰ درصد این محصول در کشورهای مذکور به علاوه عربستان سعودی، ترینیداد، روسیه و مصر تولید می شود.
- دلیل اصلی آمار بالای تولید آهن اسفنجی در چند کشور، محدود به ذخایر گاز و زغالسنگ (حرارتی)، به عنوان عوامل اصلی جهت تولید انرژی مورد نیاز فرایند احیای مستقیم مربوط می شود.
آهن اسفنجی به عنوان جایگزین قراضه و با توجه به ترکیب شیمیایی تقریباً یکنواخت آن، به منظور کاهش غلظت عناصر ناخالصی و رسوبات در ذوب از طریق بالا بردن عیار آهن موجود در شارژ استفاده می شود. در حقیقت با شارژ این محصول در سبد قراضه آهن، سطح ناخالصی های موجود در شارژ کاهش یافته و سبب کاهش مقدار نیتروژن موجود در ذوب می شود.
کاهش نیتروژن در ذوب باعث می شود، تختال ها و بیلت های با کیفیت جهت تولید ورق های گرم، وایر و انواع محصولات دیگر را بتوان تولید کرد.
مهمترین کاربرد آهن اسفنجی چیست؟
این محصول کابردهای متنوعی دارد، اما مهمترین کاربرد آن در کوره القائی است.
دلیل استفاده از آهن اسفنجی به جای آهن خام چیست؟
آهن اسفنجی عیار بالاتری نسبت به آهن خام دارد.
ویژگی های خاص گندله متخلخل چیست؟
این محصول در اندازه 4 تا 20 میلی متر تولید میشود و دارای چگالی ظاهری 3.4 تا 3.6 تن بر متر مکعب و همچنین چگالی توده 1.6 تا 1.9 تن بر متر مکعب میباشد.
بزرگ ترین تولید کننده آهن اسفنجی در دنیا کدام کشور است؟
هندوستان یکی از کشورهایی است که بهعنوان بزرگترین تولیدکننده این محصول شناخته می شود.
عالی بود خدا خیرتون بده
اهن اسفنجی چیکار به ساخت میلگرد داره ؟؟؟ چجوری اسفنجی تبدیل به میلگرد میشه دقیقا ؟؟؟ لطفا توضیح بدید
اسفنجی درداخل کوره بعداز ذوب شدن میره که شمش بشه بعدش ازشمش درفرایند گرم شدن به حالت نرم میشه ومیره توغلتکهای خط تولید میلگرد😀
سلام وقت بخیر. طبق نوشته های بالا توضیح میدم. میلگرد، از شمش آهن، تولید میشه. وقتی میخوان، شمش تولید کنن، برای اینکه، توی مذاب ، ناخالصی کمی وجود داشته باشه، بهش آهن اسفنجی، اضافه میکنن. آهنگ اسفنجی، مقدار آهن موجود توی مذاب رو، افزایش میده . یعنی آهن میاد جای ناخالصی ها رو میگیره. در نتیجه، شمش با کیفیت تری تولید میشود.
آهن اسفنجی همون کندله احیا شدس ک 92تا 98درصد اون آهن خالص چطور چ ربطی ب ساخت آهن داره اونو معمولا واسه کوره قوس الکتریکی تو شرکت فولاد خوزستان استفاده میکنیم ک حرارت نصبتا 1300درجه واسه ذوبش استفاده مسچیشه
ممکنه بفرمایید که آیا با حدود ۵میلیون دلار سرمایه گذاری جهت ساخت یک واحد کوچک تولید بیلت از گندله، ظرفیت تولید چقدر خواهد بود؟ (فقط ماشین آلات)