10 عنصر آلیاژی پر مصرف در تولید فولاد که باید بدانید
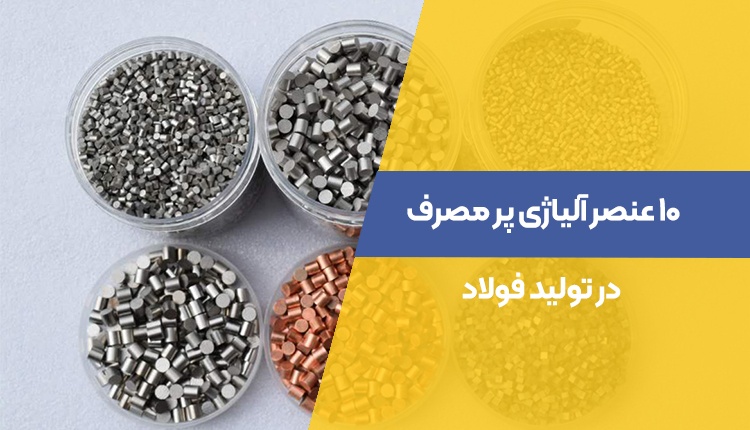
دسترسی سریع به محتوای این مطلب
عنصر آلیاژی به فلزات یا نافلزاتی گفته میشود که به منظور ساخت یک آلیاژ جدید به یک عنصر پایه اضافه میشوند تا باعث بهبود خواص مکانیکی و شیمیایی آن عنصر پایه شوند. به منظور بهبود خواص مختلفی از فولاد، عناصر زیادی به آن اضافه میشود. ما در این مطلب سعی میکنیم به بررسی 10 عنصر آلیاژی رایج که در فولاد سازی استفاده میشوند و تاثیر آنها بر فولاد صحبت کنیم. در ادامه با ما همراه باشید.
اگر درمورد آلیاژ چیزی نمیدانید، این مطلب را حتما بخوانید: آلیاژ چیست؟
1- سیلیسیوم
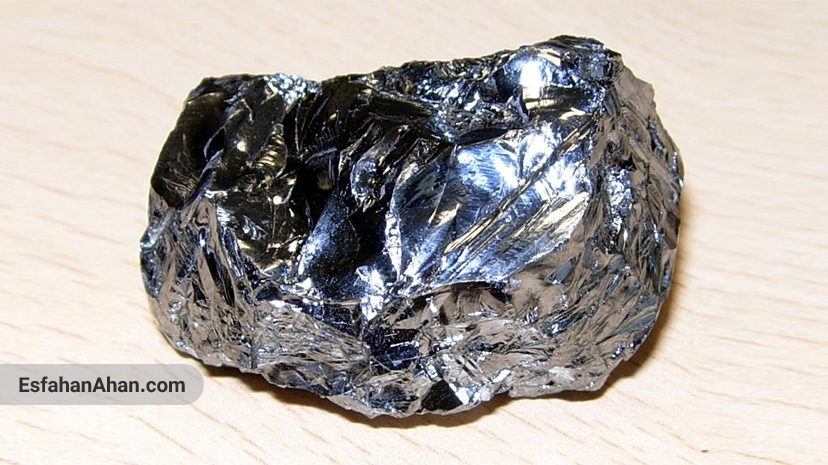
شاید سیلیسیوم را بتوان رایجترین عنصر آلیاژی در فولاد نامید، به این دلیل که تقریباً تمامی فولادها در طول فرایند ساخت به آن نیاز دارند. سیلیسیوم با دی اکسید کردن و جدا کردن دیگر ناخالصیها از سنگ آهن به خالص سازی آن در طول فرایند ذوب کمک میکند. غیر از این خاصیت خالص سازی، سیلیسیوم میتواند روی خواص مکانیکی فولاد نیز تأثیر بگذارد.
یکی از این کاربردها افزایش استحکام و قابلیت سختی پذیری و هم چنین خواص مغناطیسی برخی فولادهای خاص است. فولاد ترکیبی با سیلیسیوم شامل گریدهای مختلفی از ASTM A36 گرفته تا AISI 440C است. معمولاً فولادهای استحکام بالا مقادیر بیشتری سیلیسیوم دارند.
2- مس
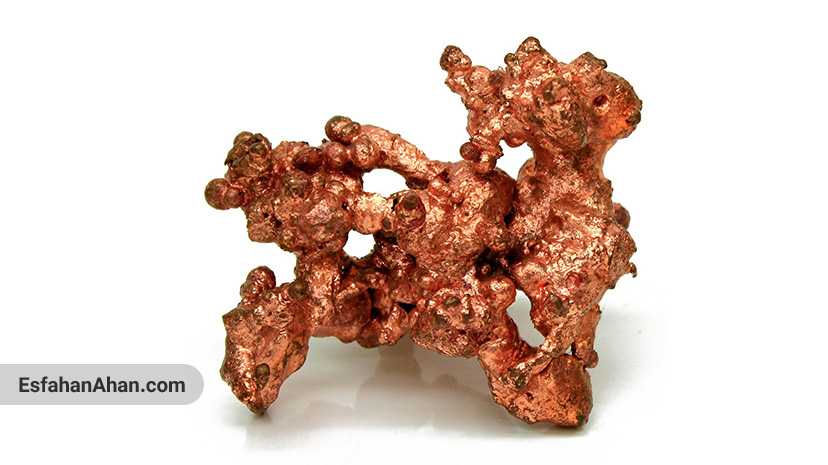
مس میتواند خواص شیمیایی فولاد را با افزایش مقاومت آن به خوردگی بهبود دهد. این عنصر آلیاژی بهطور پیوسته و در مقادیر کم به فولاد اضافه میشود. مقدار زیاد مس میتواند به جلوگیری از به وجود آمدن زنگ زدگی کمک کند. فولادهای مقاوم در برابر زنگ زدگی، در مقایسه با فولادهای کربنی استاندارد، مقادیر نسبتاً زیادی از مس دارند که از آنها معمولاً در محیط هایی که باید در معرض زنگ زدگی قرار بگیرند، استفاده میشود.
مس، خواص مکانیکی فولاد را با ایجاد قابلیت پیر سختی در آن بهبود میدهد. اما بهتر است کمی هم در مورد «فرآیند پیر سختی بدانیم. پیر سختی فرآیندی است که برای از بین بردن نابجاییها در ساختار کریستالی فلز و سپس افزایش استحکام آن مورد استفاده قرار میگیرد.
مس به مقادیر بسیار کم در فولادهای مختلفی یافت میشود. در فولاد کم کربن معمولاً مقادیر وزنی آن کمتر از 0.4 درصد است. برای مثال ASTM A36 بیشترین مقدار مجاز مس را دارد که 0.2 درصد است. مقادیر بیشتر مس در فولادهای مقاوم به خوردگی و دیگر انواع فولادهای کم آلیاژ یافت میشود، مانند: ASTM A588 و ASTM A440.
3- تنگستن:
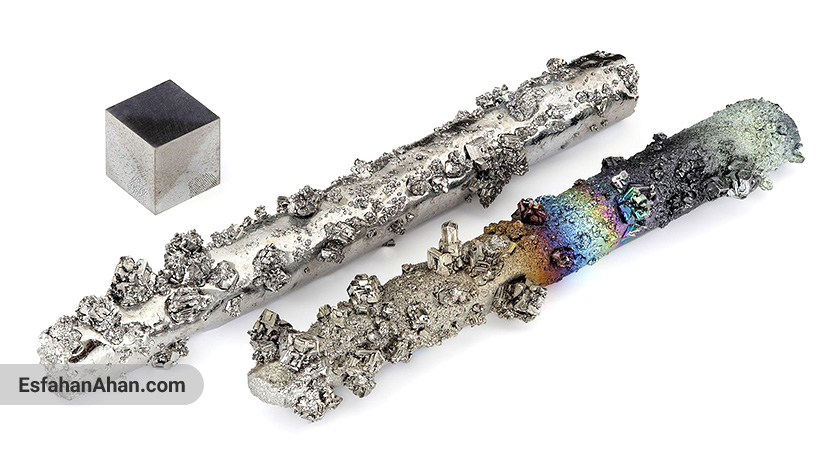
فولادها در ترکیباتشان مقادیر مختلفی از تنگستن دارند. مقداری از آن هم بهصورت باقی مانده و ناخواسته است، مانند فولاد AISI 1018. با این حال، بعضی فولادها برای بهبود خواص مکانیکی و شیمیایی در کاربردهای مختلف مقادیر اضافهای از تنگستن نیز دارند. به خاطر دمای ذوب بالا، آن (تنگستن) میتواند برای افزایش دمای ذوب فولاد نیز مورد استفاده قرار گیرد. سختی بالای تنگستن نیز مقاومت پوششی فولاد را افزایش میدهد. در نهایت، تنگستن میتواند برای بهبود مقاومت به خوردگی فولاد مورد استفاده قرار گیرد.
مقدار تنگستن در یک آلیاژ فولاد محدوده وسیعی دارد. در فولاد کم آلیاژ استحکام بالا، مقدار آن کمتر از یک درصد است. فولادهای ابزار سرعت بالا که در آنها تنگستن بهطور مکرر بهعنوان عنصر آلیاژی مورد استفاده قرار میگیرد، میتوانند مقادیر وزنی بیشتر از 15 درصد تنگستن داشته باشند. برخی از مثالهای فولاد ابزار سرعت بالای حاوی تنگستن T1,M1,M7 میباشند.
4- بور
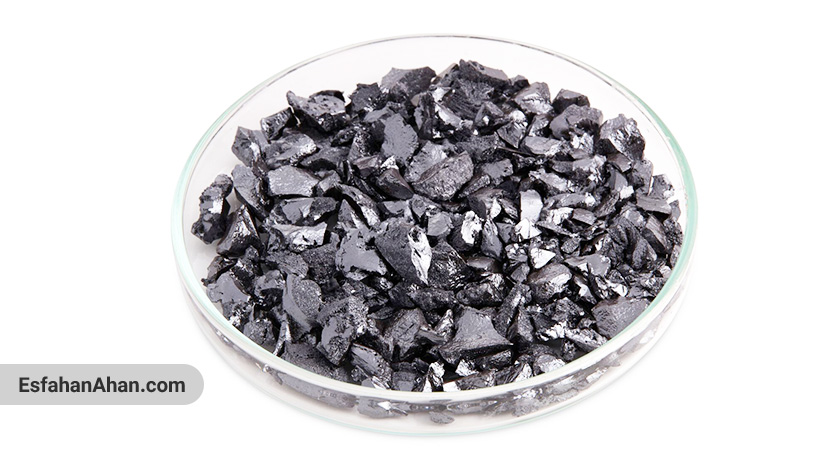
برخی عناصر آلیاژی در تغییر دادن خواص فولاد نسبت به بقیه کارآمدتر هستند. برای مثال افزودن میزان بسیار کمی از بور به اندازه حتی 0.001 درصد وزنی، میتواند تأثیر بسیار بزرگی بر خواص مکانیکی فولاد داشته باشد. خاصیت مکانیکی که با اضافه کردن بور بیشتر از همه تحت تأثیر قرار میگیرد، قابلیت سختی است. به همین در فولادهایی که فرآیند عملیت حرارتی را دارند،به طور پیوسته، بور به ترکیب شیمیایی آنها اضافه میشود.
مقادیر اضافه بور در فولاد میتواند منجر به کاهش قابلیت سختی پذیری شود، در صورتی که مقادیر بالای آن هم باعث میشود که فولاد شکننده شود و تافنس خود را از دست بدهد.
فولاد با مقادیر اضافه بور، در گریدهای مختلفی که اکثر آنها سفارشی و اختصاصی هستند یافت میشود. از فولادهای ترکیبی با بوذ میتوان به مؤلفههای مربوط به پوشش مانند ابزار زمین شناسی و میل لنگ ها است.
5- سرب
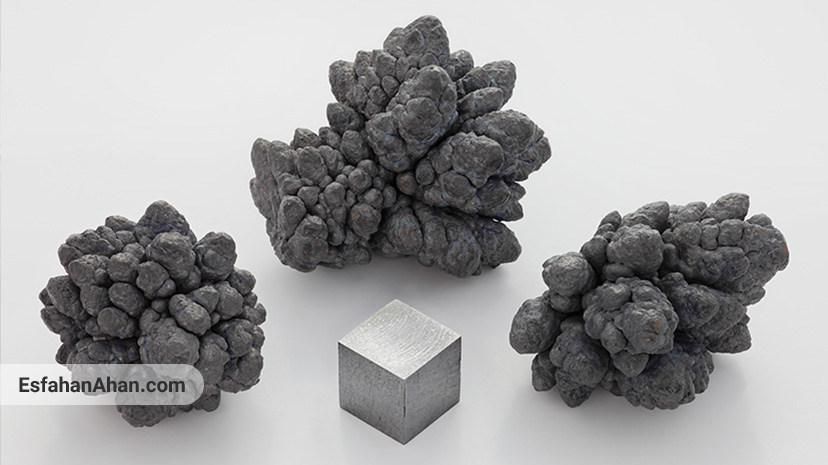
باوجود اینکه سرب، در اکثر موارد به فولادهای آلیاژی افزوده میشود، اما در واقع یک عنصر آلیاژی نیست. چرا که در زمان اضافه شدن به فولاد، به کربن، آهن یا سایر عناصر متصل نمیشود. سرب در فولاد حل نمیشود و تقریباً پس از اضافه شدن به شکل اولیه خود باقی میماند. سرب هیچ تأثیری بر خواص مکانیکی فولاد ندارد، اما چون بهعنوان روانکننده بین ابزار برش و فولاد قرار میگیرد خاصیت ماشین کاری آن را بالا میبرد.
اگر سرب به فولاد جوشکاری اضافه شود، تقریباً همیشه موجب خرابی آن میشود و اصلاً این کار را توصیه نمیکنیم.در اصل، سرب به فولاد اضافه میشود تا تحت ماشین کاری قرار بگیرد نه جوشکاری!
بد نیست بدانید که گریدهای AISI فولاد که حاوی سرب میباشند معمولاً با نماد L مشخص میشوند. آلیاژی رایج آن 11L18 و 12L14 است.
6 – کروم
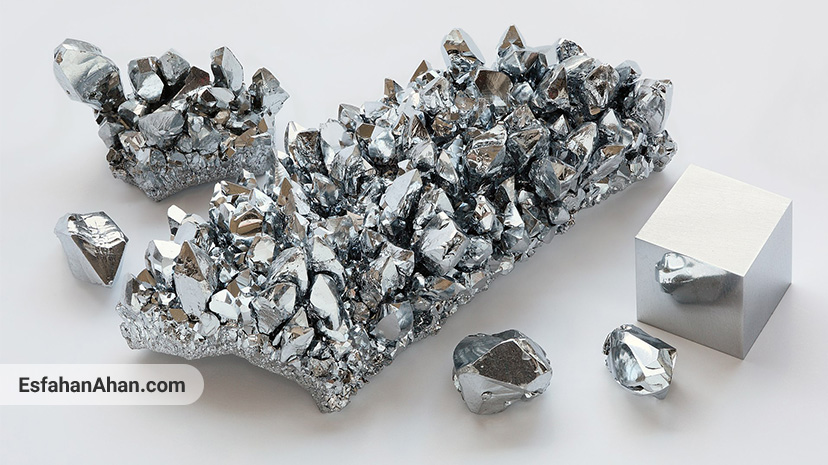
کروم معمولاً بیشتر از 11 درصد به فولاد کربنی اضافه میشود تا فولاد ضدزنگ حاصل شود. در این درصد و بیشتر از آن، مقاومت به خوردگی فولاد به مقدار قابل توجهی افزایش پیدا میکند و از اکسیداسیون آهن در شرایط مختلف جلوگیری میشود. ابتدا کروم اکسید میشود و یک لایه محافظ را روی فولاد به وجود میآورد به دلیل وجود این لایه، آهن اکسید نمیشود. کروم هر چند کم ولی به بهبود خواص مکانیکی فولاد مانند استحکام، سختی و قابلیت عملیات حرارتی کمک میکند.
فولادهای رایج با مقادیر زیاد کروم شامل فولادهای ضد زنگ گرید 439 و 309 و 225 است. فولاد ابزار گرید D2 نیز مقادیر قابل توجهی کروم در خود دارد.
7 – مولیبدنیوم
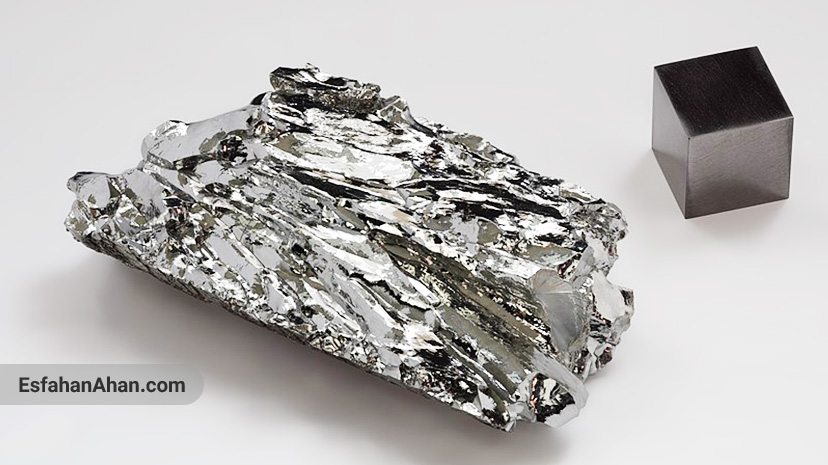
مولیبدنیوم مانند کروم بر مقاومت به خوردگی فولاد تأثیر دارد، هم چنین باعث افزایش قابلیت سختی پذیری، تافنس و استحکام کششی فولاد میشود. مولیبدنیوم خطر ایجاد حفره در فولاد را با بهبود خاصیت مقاومت به خوردگی ناشی از کلراید کاهش میدهد. میزان مقاومت به ایجاد حفره یا PRE، در واقع با ضرب مقدار ضرایب مولیبدنیوم، کروم و نیکل در یکدیگر و سپس اضافه کردن آنها به یکدیگر به دست میآید.
گریدهای رایج فولاد حاوی مقادیر زیاد مولیبدنیوم گروه A در فولادهای ابزار، فولادهای مارایجینگ مانند گرید 250 و بسیاری از فولادهای ضد زنگ دیگر است.
8 – وانادیوم
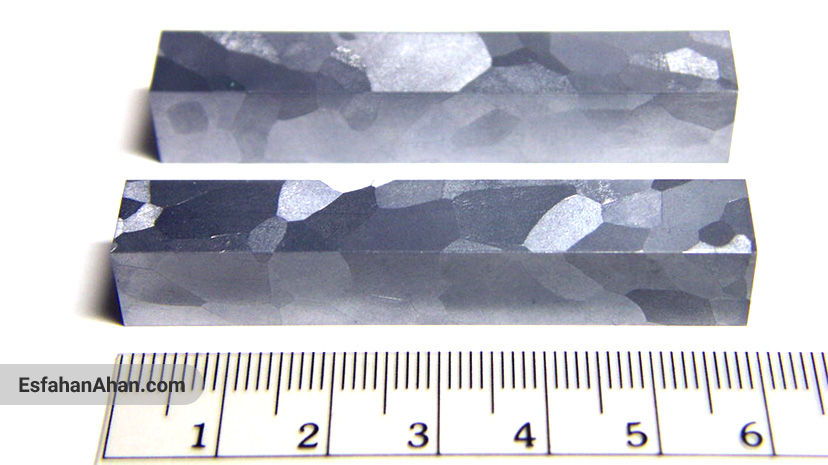
وانادیوم بهمنظور کمک به کنترل اندازه دانههای فولاد و کوچک نگه داشتن آن، مورد استفاده قرار میگیرد. دلیل کوچک شدن اندازه دانهها این است که، وقتی وانادیوم به فولاد اضافه میشود، وانادیوم کاربید شکل میگیرد و مانع از تشکیل دانهها میشود. ریز ساختار شدن دانهها به افزایش داکتیلیتی (انعطاف پذیری) کمک میکند. در بعضی فولادها، کاربیدهای تشکیل شده به وسیله وانادیوم میتوانند سختی و استحکام فولاد را افزایش دهند.
فولادهای آلیاژی نظیر A3,A9,O1 و فولادهای ابزار D2 دارای مقادیر زیادی وانادیوم میباشند. فولادهای تیغه (پره یا شمشیر) مانند M390 و VG 10 مقادیر نسبتاً بالایی از وانادیوم در خود دارند.
9 – منگنز
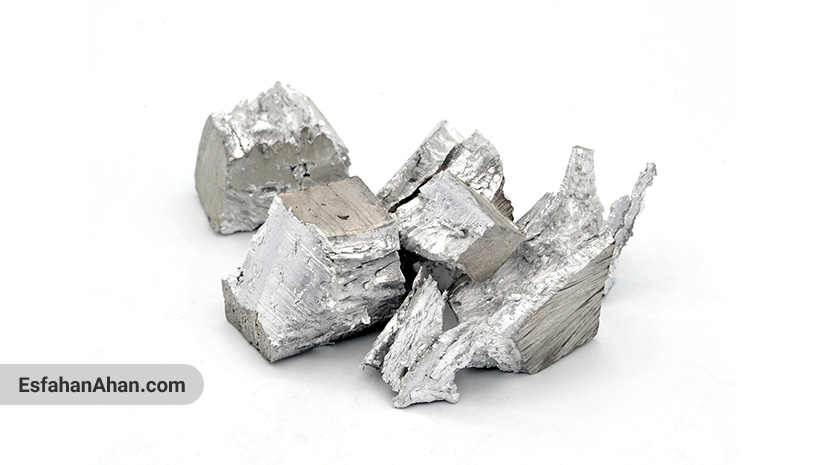
منگنز بهطور پیوسته در فولادها بهمنظور کمک به فرایند عملیات حرارتی مورد استفاده قرار میگیرند. زمانی که فولادها برای افزایش سختی و استحکام گرم و کوئنچ میشوند، نرخ سرعت کوئنچ باید بسیار بالا باشد. هر چه سرعت بالاتر باشد، فرایند ناپایدارتر میشود. استفاده از منگنز همان مقدار افزایش استحکام و سختی را به همراه دارد اما با سرعت کوئنچ پایینتر، که باعث کاهش خطر ایجاد عیب در ماده در طول فرایند گرمایش و کوئنچ میشود.
فولادهایی که حاوی مقادیر بالایی از منگنز میباشند شامل A10,A4 و فولادهای ابزار O2 هستند.
10 – نیکل
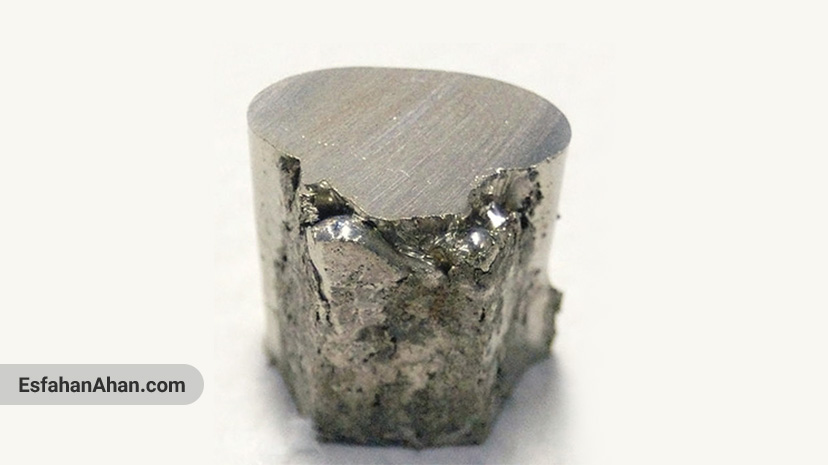
از آنجا که نیکل بهبود دهنده آستنیت است در ساخت فولادهای ضدزنگ آستنتیک به کار میرود. چنانچه مقادیر حدود 18 درصد یا بیشتر از کروم استفاده شود و ترکیب نیکل نیز بیشتر از 8 درصد باشد، فولاد ضدزنگ آستنتیک ساخته میشود. این ترکیب به شدت در برابر خوردگی مقاوم است و به همین خاطر گریدهای آستنتیک در بین فولادهای ضدزنگ بهطور وسیعی مورد استفاده قرار میگیرند. نیکل برای بهبود خواص مکانیکی فولاد نظیر افزایش تافنس و استحکام مؤثر حتی در دماهای پایین به کار میرود.
ما در این مقاله سعی کردیم در مورد “عنصر آلیاژی پر مصرف در تولید فولاد” صحبت کردیم. اگر سوال یا تجربهای در این زمینه دارید، میتوانید در بخش سوالات زیر همین مقالات سوالات خود را بیان کنید.